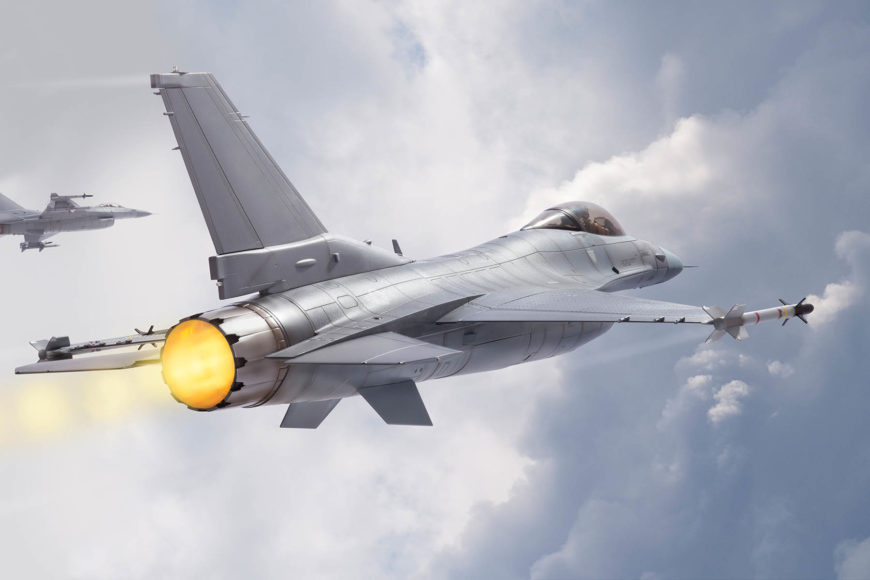
Découvrez comment une entreprise de l’aéronautique adopte l’optimisation de l’usinage CN comme moyen d’amélioration continue.
FORCE au cœur de l’amélioration continue.
La liste des équipements de Steelville comprend des tours fraiseurs Okuma LB3000 EX et des tours multifonctions Multus B300, ainsi qu’une variété de centres d’usinage à trois, quatre et cinq axes d’Okuma et de Makino. Un certain nombre d’entre eux sont reliés à l’un des deux systèmes de fabrication flexibles (FMS) de l’entreprise, dont l’un est équipé d’une cellule Fastems, considérée comme la plus longue d’Amérique du Nord. L’entreprise effectue également le pliage avec une presse, la découpe au jet d’eau, l’hydroformage, le traitement thermique certifiés Nadcap, l’anodisation et la peinture.
Les deux lignes FMS (Flexible Manufacturing System) fonctionnent en grande partie sans surveillance, 24 heures sur 24, de cinq à sept jours par semaine, une utilisation qui est selon M. Bell, a été un facteur clé de la croissance impressionnante de l’entreprise.
« Lorsque nous avons installé notre premier FMS en 2009, nous avions environ 55 personnes. En quatre ans, nous employions trois fois plus de personnes, en grande partie grâce à notre passage à une fabrication plus flexible. C’est assez incroyable ce qui arrive à un atelier après avoir investi dans un FMS. »
Adopter la vérification CN
L’ingénieur Brandon Eaton a fait partie de cette croissance. Il travaille à Steelville depuis 2013 et a récemment quitté le département de programmation pour se consacrer à temps plein à la planification des processus, à la gestion de projet et à d’autres fonctions d’ingénierie. Il continue de prêter main forte à ses collègues programmeurs lorsque l’équipe de 10 personnes est surchargée. Il estime qu’environ 200 projets par mois passent par le département. Certains d’entre eux sont des nouveaux programmes, d’autres de simples ajustements d’alimentation et de vitesse – tous sont vérifiés avec VERICUT avant d’être envoyés à l’atelier.
« Nous avons fait l’acquisition de VERICUT à peu près au moment où nos premiers centres d’usinage cinq axes ont commencé à arriver dans les ateliers. Aujourd’hui nous avons pour règle de vérifier tous les programmes CN avec ce logiciel. Il y a même eu récemment une série de projets pour lesquels le client a spécifié l’utilisation de VERICUT ou d’un logiciel similaire pour s’assurer que la pièce usinée correspondrait au modèle CAO. Pour nous la simulation est vraiment une étape importante ».
Selon M. Eaton, même les systèmes de FAO les plus performants ne vérifient pas le code G post-traité utilisé par la machine-outil. C’est pourquoi ils utilisent un logiciel de vérification indépendant afin de s’assurer de la pertinence des résultats.
« Vous seriez surpris du nombre d’erreurs que nous rattrapons. À chaque fois que nous utilisons VERICUT nous trouvons un évènement à revoir. Certes, il s’agit le plus souvent de petites modifications, comme un dépassement d’axe ou une vitesse d’avance trop élevée, mais il arrive parfois que l’on corrige ce qui aurait pu être un grave accident aux lourdes conséquences pour la production ».
Amélioration continue avec l’optimisation CN
En dehors de la prévention des accidents, M. Eaton a récemment considéré l’utilisation de VERICUT comme un outil d’amélioration continue. La réduction des temps de réglage et la prévention des temps d’arrêt des machines sont des gains évidents. Mais ces jours-ci, M. Eaton s’intéresse davantage à la capacité de VERICUT à réduire les temps de cycle grâce à son module d’optimisation FORCE.
Il affirme que ce module a permis de réduire de 20 à 43 % les temps d’usinage dans tous les programmes pour lesquels il l’utilise.
« C’est le jour et la nuit, pour les résultats », dit-il.
FORCE est un module d’optimisation de programme CN basé sur la physique.
Ce module permet à VERICUT d’analyser et d’optimiser les conditions de coupe tout au long des opérations du programme CN. Il analyse automatiquement le parcours de l’outil et compare les efforts d’usinage prévus avec une base de données spécifique au matériau. Il utilise ensuite ces valeurs pour déterminer les vitesses d’avance optimales tout au long du programme, en accélérant lorsque cela est possible et en ralentissant lorsque cela est nécessaire pour maintenir des efforts de coupe cohérents.
Toutes ces informations sont clairement visibles pour les programmeurs, ce qui leur permet de voir les taux d’enlèvement de matière, la flexion de l’outil, les niveaux de puissance et de couple. Ce module fournit à l’utilisateur une analyse proactive des programmes CN, afin qu’ils soient corrects dès la première fois.
La gestion de la vitesse d’avance du module FORCE est conçue pour maximiser l’épaisseur du copeau et la maintenir constante, en adaptant les conditions de coupe aux paramètres de performance de l’outil et aux exigences de puissance de la broche. Plutôt que d’écraser le fichier CN existant, le module crée un fichier « .opti » et le module peut ensuite afficher le fichier original à côté pour une comparaison visuelle.
« Dès mon premier essai, le module a réduit le temps de cycle de 35 % sur trois opérations d’usinage distinctes », déclare M. Eaton. « Il a également augmenté la durée de vie des outils de 150 à 200 %. C’était assez incroyable. » Cette première tâche consistait à usiner du titane Ti-6Al-4V, l’un des métaux difficiles que les développeurs de CGTech avaient en tête lorsqu’ils ont conçu le logiciel.
Selon M. Eaton, la configuration initiale de FORCE Optimisation nécessite un peu de temps.
Après cela, l’utilisation de FORCE n’était plus qu’une question de quelques clics. « Une fois en route, il suffit d’appuyer sur le bouton de lecture comme pour une vérification normale », explique-t-il.
Optimisation dans de l’Aluminium aussi bien que dans le Titane.
Après avoir réussi à usiner du titane, M. Eaton a essayé FORCE Optimisation sur une pièce à usiner en aluminium 7075-T6, dont il n’attendait une grande amélioration.
« Comme tout opérateur le sait, on peut s’en tirer à bon compte avec l’aluminium, et c’est là une partie du problème. Nous poussions les vitesses d’avance si fort que les broches décrochaient. Nous avions donc des casses d’outils avec des détériorations sur la machine.
L’utilisation du module FORCE a amélioré les choses pour l’aluminium. L’optimisation a anticipé ce problème et a réduit automatiquement la vitesse d’avance et les a pousser plus rapidement lorsque cela était possible, de sorte que même dans les matériaux plus tendres, nous avons constaté des gains énormes ».
Des résultats qui peuvent-être intimidant au premier abord.
« Nous avons essayé l’optimisation de FORCE il y a plusieurs années, lorsqu’elle a été introduite pour la première fois, et nous étions tous un peu effrayés, pensant que nous allions détériorer la machine si nous essayions d’avancer dans le titane aussi vite. Nous l’avons donc mis de côté jusqu’au début de cette année. Même maintenant, après quelques grands succès, les opérateurs sont un peu sceptiques jusqu’à ce qu’ils voient le système fonctionner. C’est un changement si radical qu’il prend les gens au dépourvu au début ».
Malgré le malaise initial, Steelville a depuis bénéficié de temps d’usinage plus rapides, d’une meilleure durée de vie des outils et de pièces de meilleure qualité.
En plus des avantages en termes de productivité, M. Eaton affirme que le module peut également aider à diagnostiquer les problèmes d’une pièce.
« Si vous voyez un tas de pics dans le diagramme de FORCE, vous savez immédiatement que vous devez reprendre un coin différemment, ou peut-être utiliser un outil différent. D’une certaine manière, cela vous permet de prendre des décisions quant à l’utilisation de stratégies de programmation différentes ».
Retrouvez notre premier article sur Steelville ICI.
Plus d’informations sur le module FORCE sont également disponibles en cliquant sur ce lien.