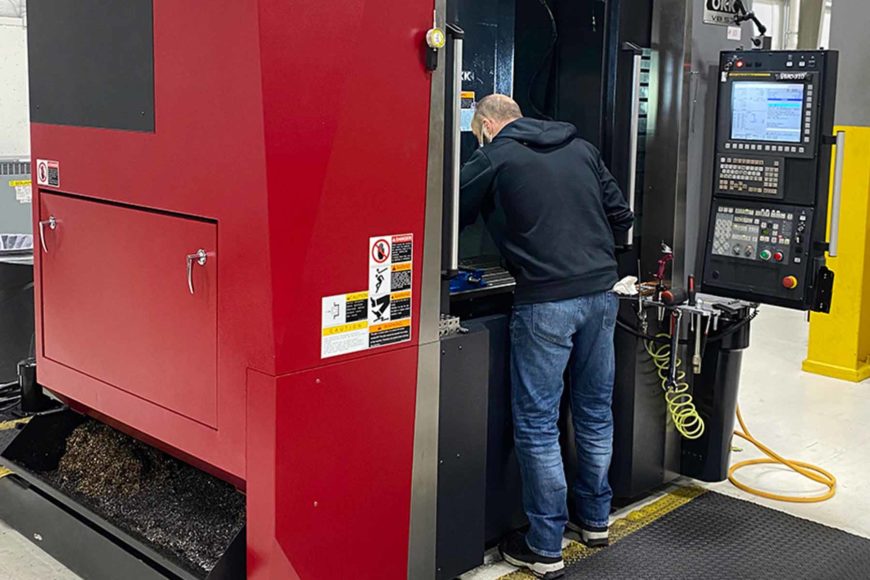
Une entreprise de conception et de fabrication de moules d’injection plastique met à l’épreuve le module FORCE d’optimisation des programmes CN. Les résultats sont surprenants.
Comment analyser et optimiser les conditions de coupe pour réduire le temps de cycle ?
De tous les secteurs manufacturiers, la fabrication de moules à injection plastique est l’un des plus difficiles. Les matériaux sont généralement durs, les géométries assez complexes et les tolérances extrêmement serrées. Avec des moules multi-cavités qui se vendent souvent pour des dizaines, voire des centaines de milliers de dollars, les enjeux sont extrêmement élevés, ce qui explique pourquoi les entreprises qui rivalisent dans ce domaine ont besoin de ce qu’il y a de mieux en termes de personnel, de logiciels, d’outillage et de machines.
Personne ne le sait mieux que les employés d’iMFLUX Inc, une entreprise de conception, de fabrication et de technologie de moules basée à Hamilton, dans l’Ohio, et filiale à 100 % du géant multinational des biens de consommation Procter and Gamble. Après des années d’efforts intensifs, l’équipe de cette société a non seulement mis au point une technologie exclusive de contrôle des processus qui améliore considérablement les résultats des opérations de moulage par injection, mais elle a également construit une installation de fabrication de moules très performante et largement automatisée.
Toujours à la recherche d’une plus grande efficacité de fabrication, iMFLUX a récemment évalué une nouvelle technologie pour augmenter les capacités d’enlèvement matière à l’atelier. Il ne s’agissait pas d’un système d’automatisation de haute technologie ou d’une plateforme de changement rapide de support de travail (ils ont déjà tout cela), mais plutôt d’un module logiciel qui réduirait les temps de cycle de 50 % ou plus tout en augmentant la durée de vie des outils et la qualité des pièces.
Son nom ? Le logiciel d’optimisation FORCE de CGTech, développeur du logiciel de simulation, de vérification et d’optimisation VERICUT.
iMFLUX Inc.
Problème :
Il fallait augmenter les capacités d’enlèvement matière de l’atelier.
Solution :
La société a investi dans le logiciel d’optimisation FORCE de CGTech – un module logiciel d’optimisation de programme CN basé sur la physique qui analyse et optimise les conditions de coupe tout au long des opérations d’usinage des programmes CN.
Résultats :
Le module FORCE de VERICUT a permis de gagner au moins 17 % sur les géométries de pièces de base et 45 % sur les géométries complexes ; il a amélioré la durée de vie des outils de manière significative avec peu ou pas d’usure des arêtes des outils de coupe; et il a amélioré la confiance des opérateurs.
Tous équipés :
L’atelier d’iMFLUX dispose d’un équipement CN impressionnant. Le côté prototypage et faible volume de l’atelier abrite des centres d’usinage OKK et Hurco, la plupart dotés de quatre ou cinq axes. Le service d’électroérosion abrite des machines à fils Makino. Des machines à mesurer tridimensionnelles (MMT) automatisées et des systèmes de vision de Hexagon et Micro-Vu sont situés à des endroits stratégiques. Tous les équipements sont disposés en configuration cellulaire pour une efficacité maximale.
Le cœur de la zone de production d’iMFLUX est sa ligne d’automatisation.
Cette ligne est remplie de centres d’usinage à cinq axes Makino V33i (20 000 et 30 000 tr/min), de stations de lavage doubles, d’une MMT automatisée et desservie par un robot linéaire et un contrôleur de cellule Erowa. « Le système transfère jusqu’à 700 pièces montées sur des palettes vers n’importe quelle station », explique Erik Morgan, responsable de l’amélioration continue « Et deux des Makino sont uniquement dédiées à l’usinage du graphite, en charge de la réalisation de 6 000 à 7 000 électrodes chaque année. »
La fabrication de moules nécessite toutefois plus qu’un bon équipement. Le programmeur Jonathon Edwards met en évidence ce qui différencie iMFLUX des autres ateliers de fabrication de moules : son personnel. « J’ai travaillé dans de nombreux ateliers au fil des ans, et c’est le seul où j’ai vu chaque opérateur avec son propre ordinateur et un logiciel de programmation complet », explique-t-il. « Certes, nous contrôlons ce qui peut être programmé et par qui, mais comme nous sommes un atelier presque sans papier et que comme nos informations proviennent du système de FAO, il est important que tout le monde y ait accès. »
Dans tous les cas, les arêtes des outils coupants optimisées par FORCE présentaient une usure bien moindre, sans aucun émoussement associé aux parcours d’outil non optimisés.
Il y a cinq ans, iMFLUX a investi dans le célèbre logiciel de simulation et d’optimisation des parcours d’outils, mais en raison de contraintes de temps liées à l’essaimage de la société de Procter et Gamble et à la croissance rapide qui a suivi, VERICUT n’a pas été mis en œuvre comme il aurait dû l’être.
Comme l’explique Gary Bare, ingénieur en fabrication avancée, tout a changé au début de 2020, lorsque lui et d’autres personnes ont convenu que la simulation devait jouer un rôle clé dans leurs processus d’usinage à l’avenir. Ils ont réévalué la décision d’achat initiale et se sont à nouveau prononcés en faveur de VERICUT.
Le développement récent de FORCE par CGTech a été un facteur déterminant dans cette décision. Ce module logiciel d’optimisation de programme CN basé sur la physique analyse et optimise les conditions de coupe tout au long des opérations du programme CN. Ce module promet des possibilités importantes de réduction du temps de cycle et d’amélioration de la durée de vie des outils. M. Edwards et le reste du groupe de la direction de fabrication ont alors pris une autre décision : vérifier si les affirmations audacieuses du développeur du logiciel tenaient la route. Utilisant la même approche scientifique que celle appliquée au reste des activités de l’entreprise, ils ont mis de côté le temps et les ressources nécessaires pour mettre Force à l’épreuve.
Pied au plancher :
L’équipe a effectué neuf tests d’usinage distincts, évaluant chaque temps de cycle, la durée de vie de l’outil de coupe et les températures de l’outil et de la pièce. Des stratégies de fraisage trochoïdal et de réduction radiale des copeaux ont été utilisées tout au long de ces essais, réalisés sur différents équipements Hurco, OKK et Makino.
Voici quelques résultats notables :
Lors de l’usinage d’une pièce en acier inoxydable 420 traitée thermiquement à 48 HRc, Force a réduit le temps de cycle de 7:51 à 4:55, soit une amélioration de 37 %. L’opérateur a utilisé le mot « impressionnant » pour décrire le parcours généré par FORCE. Sur une autre pièce fabriquée dans le même matériau, le temps de cycle a diminué de plus de deux heures, ce qui a permis à l’entreprise d’économiser sur une seule commande multi-pièces.
Plusieurs pièces présentant des parcours d’outils relativement simples ou un grand nombre de trous de perçage ont généré des économies comprises entre 9,7 % et 19,9 %. Des mesures aléatoires des copeaux ont montré qu’ils étaient « étonnamment cohérents ».
Lors du fraisage dur de surfaces complexes dans du Stavax 52 HRc, un type d’acier pour moules, FORCE a réduit les temps de cycle de 51 %.
L’opérateur a déclaré que c’était « la meilleure sonorité d’un usinage en ébauche que j’ai entendu dans notre atelier ».
L’usinage d’une pièce d’essai en P20 a permis une réduction de 30 %. Le programmeur a noté que FORCE allait « nous faire gagner beaucoup de temps et d’argent sur les outils et les interventions sur la machine ».
FORCE a également été appliqué à un programme précédemment optimisé. Cela a non seulement permis de gagner une heure sur un cycle de six heures, mais aussi de détecter et de supprimer un pic de chargement de l’outil qui aurait presque certainement entrainé la rupture de la fraise.
Dans chaque cas, les opérateurs ont inspecté minutieusement les outils de coupe après coup sous un grossissement de 72x. Dans tous les cas, à l’exception d’un seul, les arêtes des outils optimisés par FORCE présentaient une usure bien moindre, sans aucun émoussement associé aux parcours d’outils non optimisés. Dans l’un des tests où une défaillance s’est produite, il a été déterminé qu’une opération d’usinage précédente avait provoqué un écrouissage, entraînant l’écaillage d’une des arêtes de la fraise à quatre lèvres – sur l’outil sans optimisation de Force, les quatre lèvres étaient endommagées.
Outre un chargement plus cohérent de l’outil de coupe et l’élimination des pics qui conduisent souvent à la rupture, FORCE a également réduit la génération de chaleur. En mesurant à l’aide d’un thermomètre infrarouge, l’équipe d’iMFLUX a constaté que les pièces testées – usinées à sec – n’ont jamais dépassé 32°C (90°F) et que les outils de coupe sont restés en dessous de 82°C (180°F), une température idéale.
En comparaison, les pièces usinées avec des parcours d’outils « sans-FORCE » atteignaient régulièrement 300°F (149°C), créant très probablement l’émoussement mentionné précédemment.
Des conditions de coupe plus maitrisées signifient également moins de chaleur dans la pièce et la machine-outil, deux facteurs importants pour la précision des pièces.
Outre une charge plus régulière de l’outil coupant et l’élimination des pics qui conduisent souvent à des fonctionnement moins stabilisés, FORCE a également réduit la production de chaleur.
Retour en arrière :
M. Bare résume les résultats du test comme suit : « Le module FORCE de VERICUT a permis d’économiser au moins 17 %, même sur les géométries de pièces les plus basiques. Sur celles considérées comme plus complexes, des réductions allant jusqu’à 45 % étaient typiques. » Comme nous l’avons noté, FORCE a également amélioré de manière significative la durée de vie des outils, avec peu ou pas d’écaillage ou d’usure des arêtes, tandis que les températures de coupe plus basses ont réduit le gradient thermique.
Enfin, les processus plus stables de FORCE Optimisation ont eu tendance à améliorer la confiance des opérateurs d’iMFLUX et ils estiment que le retour sur investissement de VERICUT s’est effectué en à peine 1,4 mois.
Se passer de l’utilisation de l’optimisation de FORCE coûterait à l’entreprise 21 000 dollars par mois !
« Nous avons examiné de nombreuses alternatives, et je suis très heureux que nous ayons utilisé VERICUT, surtout compte tenu de ce que nous avons vu avec l’optimisation FORCE », dit Bare. « Nous avons tout mis sur la table, nous avons coché les cases de ce qui fonctionnait et de ce qui ne fonctionnait pas, puis nous avons réduit nos champs d’action. Malheureusement, nous avons perdu du temps lors de la mise en œuvre initiale, mais c’est une bonne chose que nous ayons conservé VERICUT dans l’équation. Ça a été le bon choix pour nous ».
Source de l’article : Moldmaking Technology